Journey to producing affordable, sustainable cement
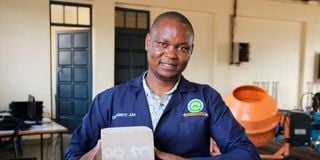
What you need to know:
Clinker, one of the main materials in the production of cement, contributes significantly to global warming. A team of researchers has, however, come up with an alternative method of making cement using clay, a largely available material.
In 2022, the Higher Education pullout of the Daily Nation reported on Dr Joseph Mwiti Marangu’s cement innovation, which would lower the cost of construction in the long term. For builders, aspiring homeowners, contractors, developers and entrepreneurs in real estate, it gave hope for a better future.
So, when will this new product hit the market?”. DN2 Property caught up with the senior lecturer and researcher as well as the director of the Institute of Cement and Concrete at Meru University. Dr Marangu is also the head of LC3-TRC Africa.
He shared some developments in the journey to making cement cheaper in Kenya, Africa and the rest of the world.
What drove you to the journey of cheap cement?
I grew up in the village. Back then, classrooms at our primary school were mud-walled. Teachers would ask us to find clay for plastering the walls during rainy seasons.
With time, the mud walls wore out and the buildings became less habitable. My curiosity grew and I wondered how these houses could be improved.
I never imagined that clay could be turned into cement. I was, however, very observant in my high school days as I attempted to understand how clay hardened when used in construction.
At what point did you start taking improvement of earthen materials seriously?
I took chemistry in my undergraduate studies. Topics like structure and bonding were really fascinating. This is where we covered the arrangement of different atoms. I began looking at the arrangement of clay atoms in different layers and the plasticity in them. It is at this point that I understood the science behind clay.
When did research on making cement out of clay begin?
I started thinking about this when I joined Kenyatta University for my master’s degree 10 years ago. For our chemistry project, we were asked to find a problem in our community that needed to be solved.
I had seen lorries transporting cement from Nairobi to the village, a very costly affair. I wondered if we could make alternative cement and whether it was possible to set up a cement factory in my home county, Meru.
That is where my research project on alternative cement began. The conversation on affordable housing had just started. Everyone in the construction industry was complaining about the high cost of cement.
I got into the laboratory and started researching and testing while consulting professionals in the cement industry. I had to first understand how the cement we used was created before moving on to produce an alternative.
I learnt that clinker was the main material in cement and Kenya imported most of it. I also came to understand that the cost of cement was dictated by the amount of clinker used in manufacturing.
However, we can lower the amount of clinker if we use alternatives we call supplementary cementitious materials. We utilise volcanic ash alongside clinker in Kenya. The problem with volcanic ash is that it is only found in specific regions, meaning production is centralised.
When you factor in packaging and transporting the cement to other counties, the cost rises. This is when clay becomes gold.
Clay is a good alternative for volcanic ash. Fortunately, it is found in every other part of the country. If you need to know how easily accessible it is, ask a nursery school child to find it. Clay is an underutilised resource with the power to solve many problems, greatly bringing the cost of cement down.
What other problems can clay solve?
Setting up cement plants in different regions will create employment and lower the cost of construction. We can even export the surplus.
There is also the issue of carbon emissions. For every tonne of clinker used, an equivalent amount of carbon is emitted. Fighting climate change by planting trees is not sustainable unless we address manufacturing. Studies show that if you have to offset one tonne of carbon dioxide emission by planting trees you need 31 to 46 trees.

Dr Joseph Mwiti, a chemistry lecturer at the Meru University of Science and Technology (MUST) shows how the compressive strength testing machine works at the main campus at Nchiru, Tigania West. PHOTO | POOL
How much space do we have for these trees? Using clay in cement-making lowers the amount of clinker required significantly, thus reducing the carbon footprint.
When was your breakthrough?
The first time we had a product that passed industry tests was in 2018. I was working with a team at the laboratory. The cement had to go through several tests, including the setting time and compressive strength. Our product had the same setting time as the industrial cement.
We also looked at the load-bearing capacity or the compressive strength test. In East Africa, it should be above 32.5 megapascals for general-purpose cement.
There is also a special category of cement, which is 42.5 and 52.5 megapascals. After 2018, we noticed that our innovation could meet that requirement for 42.5, meaning it could be used for larger industrial projects. We call it Limestone Calcined Clay Cement or LC3.
How did the name come about?
The initial challenge before 2018 was quality control. The industry has a conventional way of testing and standardising cement during production. The difference between clay and volcanic ash is that clay goes through thermal treatment for it to work. We call this calcination. If our cement was to be commercialised, the industries needed a standard, quality control process. I hit a roadblock.
But I realised there were other people around the world researching and experimenting with clay cement. I got a chance to work with researchers in Switzerland. Later, we formed a consortium of professionals in the LC3 field with members from Africa, Asia, Europe and North America.
What is the work of the consortium?
Consortium members are working together to provide answers to the many questions we have attracted and possibly reduce the time it will take for LC3 products to hit the market. While researchers would like to provide consulting support, we want manufacturers to take up LC3 and incorporate it in their portfolio of products.
We have seen an increase in inquiries by companies.
Why is the product not in the market?
The first challenge is standardisation. Coming up with a new standard requires stakeholder involvement. The Kenyan industry is fragmented as there are multiple agencies and regulatory authorities.
Fortunately, we have seen progress. I am now on the cement and lime technical committee for the East Africa Cement standards. We are working on this.
A cement factory is a massive investment. Investors need to ensure everything works to avoid losses.
How is the reception?
It is good. We held a stakeholder meeting in Nairobi last year and invited people from the cement and construction industries. Everyone loved the product. Their only question was, “When is this going to hit the market?”
Have you done testing with builders and structures?
We put up a small structure last year and it is still standing. The builders used the cement to join quarry blocks, flooring and plastering. We have also experimented with precast and interlocking blocks. They came out nicely.
Did you train the builders on using the cement?
We don’t want to train them. The idea is to hand them the cement so that they can use it as they have been doing with what is in the market. LC3 is designed to work like regular cement. We want to transition from the laboratory to the industry as smoothly and quickly as possible. Through the consortium, we have established technology resource centres to help with the transition.
The Sub-Saharan Africa Centre is at Meru University. We are leading the conversation on how other Sub-Saharan countries can set up plants for LC3 manufacture. I am in charge of the Sub-Sahara block and we operate in 48 countries.
Which of these African countries are the most proactive in taking up the technology?
We have had a lot of action in Malawi, Rwanda, Angola and Senegal. Manufacturing plants are coming up in Ghana and Cote d’Ivoire soon. They are just waiting to be commissioned.
By what percentage does LC3 lower construction costs?
If the cost of transport, availability of clay and its cost plus the lower amount of clinker used are factored in, we can reduce the cost of cement by 40 per cent. One of the business models we are considering might impact the cost significantly.
What is the cost of equipment? Are the available machines enough to support production?
Machines were a challenge at first but we identified companies that produce this category of equipment. We communicated our needs and trained them on how to address the needs. They have made the right machines.
Is the cost of these machines higher than what is already in the market?
The cost depends on how much you want to produce. This enabled us to come up with a simpler business and production model.
There are milling businesses (Kisiagi) in villages, where people go with their maize, have it ground to unga and take it home. This model is possible with our cement. With such scale of production, people can come with their clay, have it processed into cement and take it back to the construction sites.
This lowers the cost of packaging, marketing and transport. Alternatively, manufacturers can set up large plants and package cement to be sold in hardwares.
Is the LC3 limited in its application?
It can be used in all the usual processes, from flooring, plastering, slabs, concrete blocks to whichever way traditional cement is used.
When should we expect this product to hit the market?
That will depend on the country. Cote d’Ivoire is likely to be the first to start making it as early as next year.

When finally LC3 is commercialised, do you foresee challenges with consumption?
I don’t foresee a problem because the product is designed to work like regular cement. We have set up structures to make sustainable cement manufacturing successful. There is a team working at the Meru University-based centre.
More innovation and lab work are going on. Anyone can come and ask questions or have their concerns addressed. We are also organising events to bring stakeholders together.
In addition, the university introduced a department dedicated to cement and concrete. We hope to bridge the gap between academia and players in the construction industry through the department.
How old is the department and what training do you offer?
The directorate is about six months old, but we have been researching market needs for many years. We’ve had meetings with stakeholders to understand the gaps to be addressed. Of all the human needs, shelter is the most neglected. Africa has the highest rate of urbanisation and population growth in the world. The need for housing and infrastructure is still growing.
These are some of the reasons we need to build affordably and more sustainably and why this department exists. We want to focus on training, research and consultancy on the issues of cement and concrete. We are training undergraduate and graduate students on cement and concrete technology. To bridge the gap between theory and practice, we offer short courses to people already practising.
We’ve noticed that most people working in construction learn about cement on the job. Cement is a mystery. People do not understand the chemistry of cement hardening after putting in water.
Your parting shot?
Let industry players know that we cannot talk about affordable housing without addressing the cost of cement. If we want to make housing truly affordable, we need to unpack the issues. Stakeholders have addressed financing, access to land and loans.
That, however, is just a fraction of it. When we get down to all the elements of an affordable house, we will arrive at the cost of cement. A large percentage of construction work involves cement, whether it is residential and commercial houses, roads or dams. We need to have a dialogue about affordable cement. Clay is a solution and we have plenty of it.