‘Made in Kenya’: We don’t have to reinvent the wheel
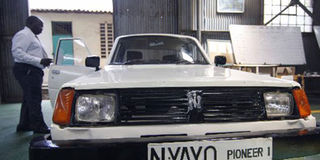
The Nyayo Pioneer car made in Kenya in the 90s. No African country maintains reliable records on training and deployment of engineers. PHOTO/FILE
What you need to know:
- But there is no such integrated car “Made In” anywhere. Every vehicle that is or ever was has been made by dozens of different companies using materials from dozens of different countries.
- On a car rolling out of a factory gate for, say, Sh2 million, what proportions of that money go to the rubber and cotton plantations and oil wells and iron mines where the raw materials originated, what proportion to the various secondary processors of rubber, fibres and textiles, plastics and steel; what proportion to the tertiary bunch who turned those processed materials into components, and what proportion to those who put all those bits together as a finished vehicle?
The popular presumption is that motor manufacturers are giant factories that receive raw materials, process them into components, and then assemble them into a vehicle.
But there is no such integrated car “Made In” anywhere. Every vehicle that is or ever was has been made by dozens of different companies using materials from dozens of different countries.
All motor manufacturers “source” what they need – be it a raw or semi-processed material, or a completely finished component – from all over the place.
All of them, without a single exception, are giant versions of what we call “Vehicle Assembly Plants”. They vary in size. They vary in their degree of national or international networking or shareholding and in their degree of industrial processing.
What they also do, constantly and universally, is copy each other. A Frenchman, in France, invented the pneumatic tyre – but probably using a pencil made in Germany and paper made in Sweden, and manufactured it using fibres produced in India and woven in Italy, with rubber grown in Malaya and cured in Spain, on factory machinery with equally diverse sources.
FINISHED PRODUCT
In reality, something is “made” in the place where it becomes a finished product in its final form, having undergone some substantive manufacturing and/or assembly process in that place.
It also depends (a bit) on where the brand name it bears is from and (a lot more) on where the main “value” of the finished product is generated.
On a car rolling out of a factory gate for, say, Sh2 million, what proportions of that money go to the rubber and cotton plantations and oil wells and iron mines where the raw materials originated, what proportion to the various secondary processors of rubber, fibres and textiles, plastics and steel; what proportion to the tertiary bunch who turned those processed materials into components, and what proportion to those who put all those bits together as a finished vehicle?
Where international trading deals apply different duties to vehicles “Made In” one place as opposed to another, the benchmark value portion is around 35 pc.
Pick any “new” make from any corner of the globe, and trace its history. You will find it started as a joint venture with an existing major automaker, initially assembling an absolute clone of the original product; then putting a new badge on it.
Thence – supported by massive policy commitment, and investments – steadily increase the degree of local content and progressive manufacture to a point of export potential and eventually even starting to dabble with unique design changes.
Kenya has done all that for more than 30 years now, although policy has sometimes driven the idea with its foot firmly pressed on the brake pedal. But if we want to make more of our own cars or make our own cars even more completely, we already know what must be done, and how to do it.
We don’t have to reinvent the wheel in order to manufacture one “Made in Kenya”.