How varsity students are turning agriculture waste into clean products
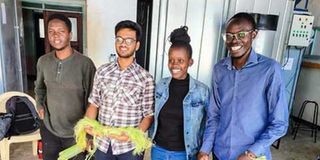
Vincent Momanyi, Mitesh Varsani, Noreen Mwancha and Charles Oyamo.
It started just as an idea for four university students in 2022.
The plan was on how they could make good use of agricultural waste by turning pineapple leaves, sugar cane bagasse and corn husks into economically usable products, while helping farmers get rid of the waste from their farms.
Then early 2023, determined to actualise the idea but unable to fund its practice, the team of students from the University of Nairobi (UoN) and Kenyatta University (KU) decided to venture into competition to get capital.
By the end of February, they went to Olare, Homa Bay County, to engage pineapple farmers, kick-starting an enterprenuership.
The team was more determined to move along with and see Kenyans wear clothes, shoes or decorate their vehicles out of fibres made from a process they have innovated.
They incorporated a company called Rethread Africa, and its core activity is turning agricultural waste into fibres that are used in making clothes, foot wear and upholstery for materials including the interior of a vehicle.
“When we started, we were working around sugarcane bagasse and corn husks. I come from Migori county where we grow sugarcane and maize a lot. I needed to do something that could improve the livelihoods of people in my community,” recalls Mr Charles Oyamo, a final year student at UoN.
And so together with Vincent Momanyi and Mitesh Varsani, both UoN students, and Noreen Mwancha, a second-year student from KU, the four embarked on a journey they now say has been offering much learning as well as growth.
Over the past four months, engaging a group of farmers in Homa Bay County, they have processed at least 150 kilogrammes of pineapple leaves to make fabric that can be used in making clothes.
They say they have now proved that, indeed, their concept to make locally made clothes from agricultural waste is possible and rolling out the initiative on an industrial scale by the end of this year.
“We are continuing in Research and Development (RND) in sugarcane bagasse and corn husks but we are going to commercialisation with pineapple leaves. Today we’ve been able to produce about 150 kilogrammes of pineapple leaves that have yielded about two square meters of fabric,” Mr Oyamo says.
The fabric-making process begins at the farm where, through a model farmer, farming communities- organized as groups of farmers within a 30-kilometre radius- take the agricultural waste to the homestead of the model farmer, where the company places its equipment and runs the processing of the waste to fabric.
Pineapple leaves can be harvested between 12 and 18 months, which helps the fruit get even healthier when leaves are reduced and more nutrients are directed to the fruit.
The leaves are then sorted before being taken through an extractor, where they are fed into the machine and on the other end comes out fibres and other plant materials that can be used as compost at the farm.

Mitesh Varsani, Vincent Momanyi and Charles Oyamo at the extraction stage of pineapple leaves.
The fibres are then washed and dried before being spinned into a yarn, after which they are ready to be sold to a weaving facility.
“We are now done with the pilot stage. We’ve proved scientifically that this works, we now plan to transform the pilot programme at an industrial scale by taking in more waste, of different types, through the same process. In terms of an end product, over the next six months, we are looking at having dresses, shoes, shirts and jackets made from our material so that people are able to see, feel and touch it,” Ms Mwancha says.
They are in the process of acquiring equipment that will facilitate the processing of corn husks, sugar cane bagasse and other natural fibres into economically usable alternatives, and at large scale.

Fibre drying on a hanging line after cleaning.
Recently, they won a prestigious Global Change Award- for their initiative due to its potential to rid farmers of the agricultural waste while making innovative products that can transform the fashion industry to become planet positive. It was awarded Sh29 million. The team says the money will enable them expand to operate large scale and on a more sustainable basis.
While they do not envision venturing full scale from collecting waste to making final products, they believe that the role they play is key as it will provide raw materials for Kenya’s apparel industry and boost the local garments industry.
“Our skills and expertise lies in research and development, figuring out different types of wastes and processes they need to go through to get to the fabric stage. Then others can take over and make shoes, clothes, bags and other items,” Mr Oyamo says.
In recognition of the role they play at the value chain, the company has been reaching out to potential partners who can buy their fabric. It believes the partnership will be key to their success in the market. Partnerships are its route to the market, it says.
“We are in conversations with a lot of interested players including Hugo Boss after they reached out to us and a brand called Savannah Sands looking at how our materials can be used for bags, accessories and upholstery,” Ms Mwancha says.