Engineer Charles Maitha keeps dairy farms mechanised
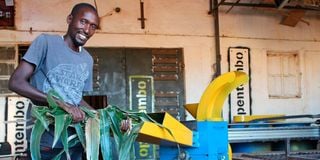
Charles Maitha shows how he makes silage choppers, starting with computer designs to fabrication in the workshop in Makindu, Makueni County.
Tens of trucks destined for the neighbouring countries line up on the main streets of Makindu, a town on Mombasa-Nairobi highway.
The heavy commercial vehicles ferry export products from the port of Mombasa to Uganda, Rwanda and the Democratic Republic of Congo (DRC), among other nations.
Makindu is one of the towns where the drivers make a stop, what has made the urbanising centre vibrant.
Charles Maitha is one of the businesspersons competing for space with the trucks in the town.
Maitha, who manufactures assorted agricultural machines, runs a workshop on a dusty street that overlooks the vehicles’ parking bay.
Seeds of Gold team finds the mechanical engineer supervising workers putting final touches on three silage choppers ready for sale.
“We tailor-make machines for small and medium agribusiness ventures,” Maitha, 40, says as he shows the Seeds of Gold team around the busy workshop, which also serves as his office.
On a normal day, Maitha’s work at the workshop entails talking to clients and translating their requirements into drawings. First on paper and then using computer applications, as well as working closely with a team of three artisans and a mechanical engineer to design and execute new projects.
He also markets finished products through social media. A lot evidently goes on at the workshop but telling from the work in progress, the silage chopper-cum-grain grinder is the popular machine he makes.
The machine is composed of a frame, which has provisions for fixing an electric motor or diesel generator, grain and silage hoppers and the main body, which houses the grain grinding and silage chopping mechanisms.
Nuts and bolts
Save for the motor and the nuts and bolts, all the other parts are fabricated on site. The work starts with designing the machine and all its components using computer applications.
“We then use a plasma-cutting machine to cut all the parts for precision. The chopping mechanism uses a combination of knives made of hardened steel and flexible hammers, which ensure that particles that escape the knives are crushed,” he explains.
“The flexible hammers form the bulk of the grinding mechanism. They repeatedly hit the grains to the desired dimensions. A simple metal plate is all that is required to switch from the chopping to the grinding function by blocking the chopping inlet,” he adds, showing understanding of the engineering work he has been doing for the last six years.
Maitha started the enterprise in 2015, seven years after graduating from Egerton University with a major in manufacturing engineering and technology. In between, he designed computer applications for banks, dealers in motor vehicles and water companies.
At some point, he worked at Equity Bank where he was charged with designing its main banking system. A burning desire to be his own boss saw the restless Maitha quit formal employment.
After relocating to Makindu, he set up a small workshop that specialised in general fabrication. Although he still consults for the bank and other clients, Maitha’s heart has been in manufacturing agricultural machines. His main source of inspiration is Akinwumi Adesina, the president of the African Development Bank who believes farmers are the next generation of billionaires.
In Makindu, Maitha is one of the young agripreneurs who are slowly industrialising the town. The other is Victor Sila, who has set up a yoghurt manufacturing factory in the town that makes Uzima yoghurt.
A Sh1.5 million automatic machine for dispensing yoghurt into plastic cups and sealing using aluminium foil powers the business. The machine is one of Maitha’s handiwork.
Parts of motorcycles
Although Maitha has a lucrative deal for making some parts of motorcycles with a local company that assembles the machines imported from China, he maintains that his business is hinged on the silage chopper-cum-grinder.
“The chopping mechanism does not allow green silage to stick to the knives. This prevents the damaging of the electric drive. The machine chops between 500 and 3,000 kilos of 16mm size silage per hour. For the last one year, we have sold more than 100 pieces at Sh40,000 each,” he says.
Maitha makes the machines in batches. The last time he did a batch of 40 pieces in 20 days.
Besides the rising cost of raw materials, which eat into his profits, Maitha has to contend with potential clients who grow cold feet upon realising the workshop is located in the countryside. He uses courier service to deliver to customers.
Through EMS Kenya, it costs Sh3,500 to sent a machine from Makindu to an address in Rift valley, which takes two working days. A tracking code is also shared with the client for tracking.
Prolonged drought
The growing demand for chaff-cutters can be linked to rise in the number of small-scale dairy farms. Weary of the high cost of feeds, which experts link to the prolonged drought and the invasion of Ukraine by Russia, dairy farmers have switched to silage, which they prepare at home.
There has also been an aggressive campaign for farmers to embrace silage as a feed amid climate change as well to mechanise farms.
Mechanisation unlocks the potential of agriculture value chains, according to Paul Woomer, a technician at Technologies for African Agricultural Transformation, which is among the development agencies that have been at the forefront of championing uptake of machines among smallholder farmers.
“Mechanisation makes agriculture sustainable by enhancing production while cutting down on the costs. Machines make agriculture attractive to young people and create more opportunities in the industry,” he says.
Lack of capital is among the barriers that hinder small farmers from buying machines.
Maitha’s wide range of after-sale services come to the rescue of farmers who decry lack of technical services and high cost of maintenance of machines. “Instead of buying many machines, a farmer should consider buying one machine which comes with more attachments to perform multiple functions. Farmers should also consider coming together in groups and cooperatives to acquire machines,” Dr Woomer advises farmers.